前回(第5回)は、評価CAEの概要と課題について以下のように紹介しました。
評価CAEは構造系に始まり、機構系、流体系へと対象領域を拡大し、開発手戻りの防止に貢献してきました。一方で、CAEによる解析や評価が難しい技術課題が残されており、実機検証に依存せざるを得ないため手戻りにより開発効率やスピードのボトルネックとなる恐れがあります。
今回(第6回)は、自動車用エンジン開発においてCAE評価手法が未確立な技術課題を例に、評価CAEの課題解決手法について解説します。
エンジン(ハードウェア)の耐久信頼性に関する不具合を簡略化し、便宜的に以下の4項目に分類します。今回の対象は(2)劣化型で、経年変化により不具合が発生するケースです。
(1)強度型: 構造部品の破損に代表される不具合で、概ねCAE評価手法が確立されています
(2)劣化型: 摺動部品の摩耗に代表される不具合で、一部はCAE評価手法が未確立です
(3)機能型: システム機能の不具合で、MBD手法を用いた評価手法が確立されつつあります
(4)その他: 上記以外の不具合で、頻発する課題についてはCAE評価手法が確立されています
劣化型不具合が発生しやすい代表例として、エンジン潤滑システムについて解説します。
エンジン内部には、主運動システム(クランクシャフト、コネクティングロッド、ピストン等)や動弁システム(カムシャフト、ロッカーアーム、バルブ等)等、多くの運動部品があり、運転中は常に摺動しているため接触面圧や相対速度等に応じて、それぞれ適切な潤滑が必要です。この潤滑機能を担うのが潤滑システムで、潤滑油がオイルパン→オイルポンプ→オイルフィルター→各摺動部品→オイルパンという回路を循環しています。
過酷な運転条件下では摺動部に油膜切れが発生し、過度な摩耗や焼付きに至ることもあります。その要因は相対挙動、表面性状、給油状態等多岐に渡り、解析や評価が難しいシステムの一つです。近年ではCO2削減の一環で摩擦損失低減が求められ、潤滑油量の削減や潤滑油の低粘度化が進み、さらに厳しい潤滑状態になりつつあります。
潤滑システムにおける不具合のメカニズム解明の第一歩として、潤滑油挙動の把握が不可欠です。エンジン内部では各部品給油後に気液混相状態となり、運動部品により潤滑油が撹拌されて飛沫も多く、実機での潤滑油挙動の可視化には限界があります。加えて、従来の流体系ソフトでは解析に時間がかかるため、量産開発中の解析は容易ではありません。一方、気液混相解析に強く、メッシュフリーで高速解析が可能な粒子法ソフトの代表格であるParticleworksが進化し、機構系CAE(RecurDyn)との連成解析も実現したことで突破口が開けました。実機を模擬した単体実験の結果と合わせ込むことで潤滑油挙動を概ね予測できるようになり、パラスタによる給油条件の最適化も十分可能になりました。
以下に、Particleworksを活用した潤滑油挙動解析例を紹介します。
①チェーン給油解析
エンジンのタイミングチェーンは、クランクシャフトとカムシャフトの回転を同期させる部品です。給油条件等が悪ければ摩耗が進み、許容限度以上の伸びが発生する恐れもあります。機構・粒子法連成解析により、チェーンおよび供給される潤滑油の挙動を運転条件毎に時系列で可視化でき、解析や評価が可能になりました。右図はParticleworksとRecurDynの連成解析例です。
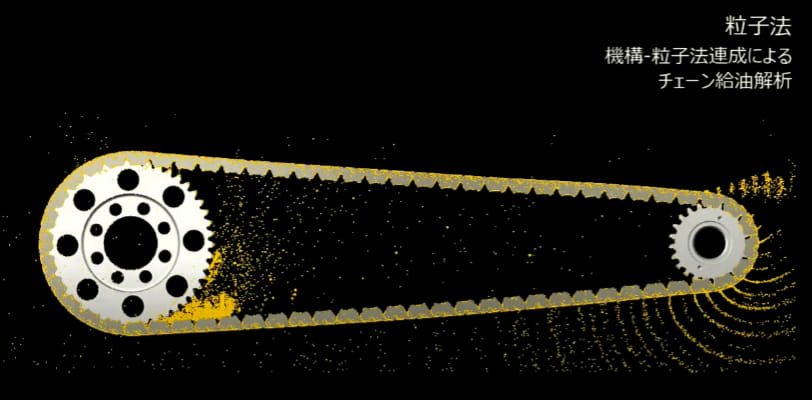
提供:株式会社ファソテック
②ピストンオイル冷却解析
ガソリンエンジンのノッキング(未燃混合気の一部が加熱されて自己着火し急激に燃焼する現象)を抑制するため、ピストン頭部にクーリングチャンネル(円環状の空洞)を設け、オイルジェットから潤滑油を供給し撹拌効果でピストンを冷却します。機構・粒子法連成解析により、チャンネル内の可視化も含めて解析や評価が可能になりました。右図はParticleworksとRecurDynの連成解析例です。
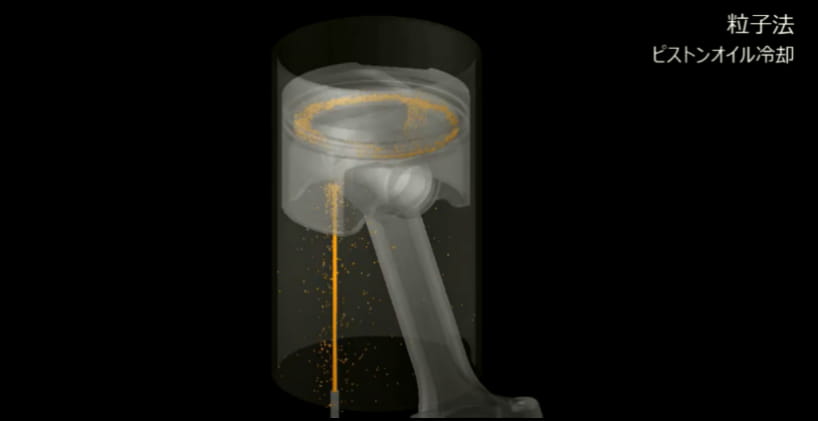
提供:株式会社ファソテック
CAE評価手法が未確立な技術課題の解決手順について解説します。メカニズム解明にはパラメータ感度が鍵となります。開発現場では時間の制約があり、スピーディに実用的な解を得ることも重要です。
一般的な解決手順の流れと要点は以下の通りです。
解決手順:
(1)協業体制構築と資源確保 → (2)パラメータ感度解析とメカニズム解明 → (3)設計基準確立 → (4)CAE評価手法確立 → (5)プロセス標準化
(1)協業体制構築と資源確保
・CAE単独での解決は難しい課題も多く、各部門(設計、解析、実験)の協業が必要です。
・マネジメント層の理解を得て協業体制を構築し、開発資源(要員、設備、予算)を確保します。
・技術課題が複数ある場合は、優先度を定めて継続的に解決していくことが重要です。
(2)パラメータ感度解析とメカニズム解明
・不具合発生要因を体系的に抽出した上で、知見に基づき主要因を選別し現実的な数に減らします。
・時間短縮のため、実機を模擬した単体実験で主要因毎のパラスタ(各3水準)を実施します。
・実験データに基づきパラメータに対する感度解析を行い、感度の高い要因を特定します。
・パラメータ間の交互作用が疑われる場合は、必要に応じて品質工学手法を用いて追解析します。
(3)設計基準確立
・実験結果を基に実験式を作成します。実験範囲内であれば劣化等の予測が可能です。
・設計基準(設計で守るべき定量的な基準)の一つとして整備し、設計パラメータ選定時に活用します。
(4)CAE評価手法確立
・適切なCAEを選択し、実験結果と合わせ込み実用的なCAE評価手法を確立します。
・まず感度を確実に合わせ込み、次に絶対値を合わせ込みます。
・実機との精度検証を十分に行うことで、実験式よりも広い範囲で予測可能になります。
(5)プロセス標準化
・開発現場での安定した運用やトレーサビリティ確保のため、構築したプロセスを標準化します。
・プロセス標準化のポイントは、“SIPOC”および“RFLP”です(第3回で解説)。
デジタルエンジニアリングの一環として、実験依存からの脱却を目指してCAE評価手法を確立することが重要です。そのためには各部門(設計、解析、実験)の協業による継続的な活動が必要です。本活動を通して部門の壁を超えた総合的な知見や課題解決手法が体得でき、エンジニアには貴重な経験になることと確信しています。次回(第7回)は、企画CAEの概要と課題について解説します。
INDEX
第1回 序 略歴とコラム紹介
第2回 DXとデジタルエンジニアリング
第3回 製品開発プロセスの目指す姿
第4回 DX時代のCAE
第5回 評価CAEの概要と課題
第6回 評価CAEの課題解決手法
第7回 企画CAEの概要と課題
第8回 企画CAEの運用と応用
第9回 設計CAEの概要と課題
第10回 設計CAEの課題解決の進め方
第11回 開発プロセス運用の仕組み作り
第12回 まとめと変革の時代に求められるエンジニア像
著者ご紹介
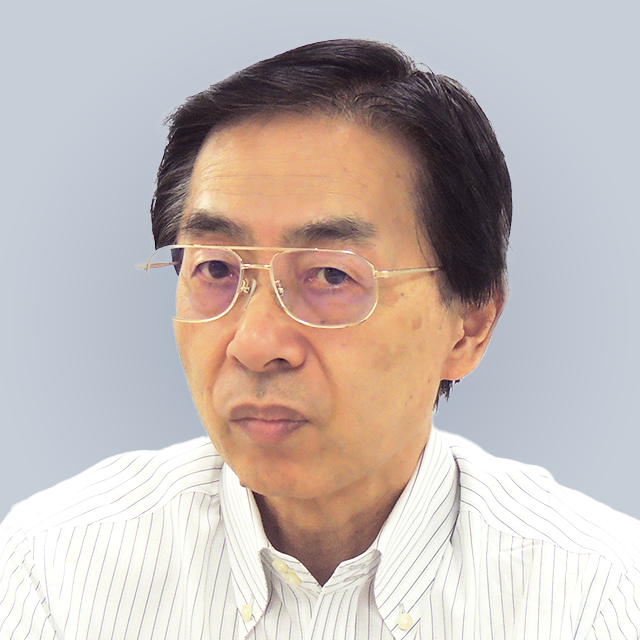
品川エンジニアリング株式会社
(技術コンサルティング)
品川 博 様
プロフィールを見る
1979年
㈱本田技術研究所 入社(四輪R&Dセンター)
- エンジン設計(基幹部品)
- エンジン設計部門長
- パワートレイン開発部門長(米国研究所)
- 開発プロセス改革(MBD/MBSE、設計基準構築等)
2016年
品川エンジニアリング㈱ 設立(技術コンサルティング)
- MBD/MBSE、開発プロセス改革等