前回(第9回)は、設計CAEの概要と課題について以下のように紹介しました。
設計プロセスを支援するのが設計CAEであり、MBDやCAE等を駆使することで製品設計プロセスが大きく進化します。設計者には設計CAEの価値を十分に理解し、企画部門や解析者と連携して課題を乗越え、製品設計に積極的に活用していくことを期待します。
今回(第10回)は、設計CAEの課題解決の進め方等について、前回同様に自動車用エンジン開発(ハードウェア主体)を例に、以下の2項目を取り上げて解説します。
①自動車会社(企画)とサプライア(設計)のプロセス連携
②設計最適化(構造最適化)プロセスの構築
①自動車会社(企画)とサプライア(設計)のプロセス連携:
自動車会社は多くのサプライアと協業し自動車を開発製造しています。一部のシステムでは自動車会社が企画からシステム構想設計程度までを担い、サプライアがシステムの設計開発と製造を担うシステムサプライアの存在感が次第に大きくなっています。サプライアにおいても手戻りの無い高効率な開発等を目指してMBDの導入が進められ、自動車会社とシステムサプライアのプロセス連携も始まっています。
以下はプロセス連携の一例で、MBDを武器に、より精度の高いシステム開発が実現しつつあります。自動車会社は、企画時に車両要求を基にシステム仕様書(各種要求)やシステム構想設計(基本レイアウト)等に加えてエンジンモデル(簡易モデル)を作製し、サプライアに発行します。サプライアは、発行されたエンジンモデルを自社システムモデルに接続し、要求を満足するようシステム性能設計を行います。次に、システム(1D)から部品(3D)につなぎ、提供された構想設計を基に制約条件(製造要件や耐久信頼性等)内で構成部品の詳細設計を行い、仕様や売価等を整理した上で製品システムを自動車会社に提案します。
なお、自動車会社がシステム開発を担い、システムを構成するサブシステム開発をサプライアが担うケースもあります。自動車会社がシステムモデルにサブシステムモデルを接続してシステム性能設計を行う必要がありますので、企業間のモデル連携や流通の仕組み作りの検討も進められています。
②設計最適化(構造最適化)プロセスの構築:
部品の軽量化等を狙いとした3次元の設計最適化を例に、基本的な進め方等を解説します。設計最適化手法は、大別してパラメトリック最適化とノンパラメトリック最適化の2つの手法があります。一般的に軽量効果は設計自由度次第で、制約条件(設計空間や製造プロセス等)が少ないほど効果が大きくなります。近年では3Dプリンターが進化し、制約が少ない製造手段として評価されています。現時点では大量生産や耐久性が重要な強度部品等には課題が残されていますが、少量の意匠部品等に採用例も出てきました。両手法共に、システム性能に影響を与える部品や多目的最適化(多機能で目的関数が複数存在)となる部品への適用には工夫が必要になります。
パラメトリック最適化は、CAD機能を利用して設計パラメータを振り最適構造(形状)を求める手法です。既存の設計構造からは大きく変わらないため軽量効果には限界もありますが、適用例が増えています。3Dの最適化は時間もかかるため、CADとCAEを連成させて最適化ソフトでワークフローを組み、繰返し計算を自動化して大幅な時間短縮を実現した事例が報告されています。
流体系のパラメトリック最適化(流路の最適化等)については、従来の格子法ソフトではメッシュ作成も含めて時間がかかり、現場での活用には限界がありました。一方、メッシュフリーで各種連成解析も可能なParticleworksに代表される粒子法の登場と進化により現実的な時間内で最適化が可能となり、今後の設計への活用拡大が期待されています。右図は、加工液の濾過システムにおいて、内部のコーン形状を最適化することでスラッジの濾過効率を最大化した事例です。
ノンパラメトリック最適化にはトポロジー最適化やジェネレーティブデザインと呼ばれる手法等があります。トポロジー最適化は基となる構造(形状)から最適化を行う手法で、ジェネレーティブデザインは自動的に最適な構造を作成する手法です。いずれも、従来の設計には無い新たな構造を発見するためには有効な手法です。ちなみに、設計最適化は設計行為の一環であり、設計者はデザインレビュー等で設計の技術根拠を説明する責務があります。設計者にはノンパラメトリック最適化アルゴリズムの理解は難しくブラックボックスとなる恐れもありますので、初めにノンパラメトリック手法で基本構造を絞り込み、次にパラメトリック手法で詳細構造を定める二段階の最適化アプローチも検討されています。
軽量化ニーズは設計現場に広く存在し、設計者が利用可能なソリューションが求められています。CAEツール単独で軽量化を実現することは難しく、複数のツールや手法を組合せて汎用的な設計最適化プロセスを構築することが必要になるでしょう。
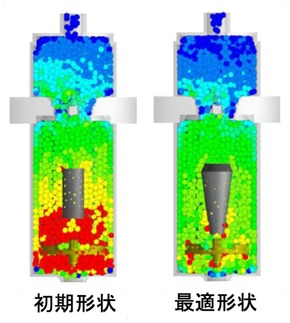
企画プロセスから始まったMBDの普及拡大と共にデジタル技術を駆使することで設計プロセスも進化し、将来の製品開発プロセスの姿が明らかになってきました。プロセス連携や最適化等の課題は残されていますが、新たな設計プロセスと支える設計CAEの確立に向けて着実に努力が重ねられています。
次回(第11回)は、MBD手法に基き再構築した開発プロセスを開発現場で確実に運用するための仕組み作りについて解説します。
INDEX
第1回 序 略歴とコラム紹介
第2回 DXとデジタルエンジニアリング
第3回 製品開発プロセスの目指す姿
第4回 DX時代のCAE
第5回 評価CAEの概要と課題
第6回 評価CAEの課題解決手法
第7回 企画CAEの概要と課題
第8回 企画CAEの運用と応用
第9回 設計CAEの概要と課題
第10回 設計CAEの課題解決の進め方
第11回 開発プロセス運用の仕組み作り
第12回 まとめと変革の時代に求められるエンジニア像
著者ご紹介
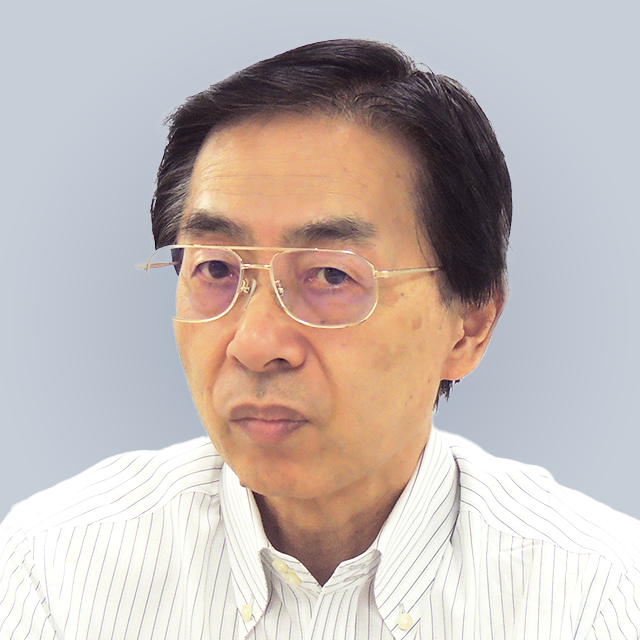
品川エンジニアリング株式会社
(技術コンサルティング)
品川 博 様
プロフィールを見る
1979年
㈱本田技術研究所 入社(四輪R&Dセンター)
- エンジン設計(基幹部品)
- エンジン設計部門長
- パワートレイン開発部門長(米国研究所)
- 開発プロセス改革(MBD/MBSE、設計基準構築等)
2016年
品川エンジニアリング㈱ 設立(技術コンサルティング)
- MBD/MBSE、開発プロセス改革等